First published in PTQ Q4 2017
Eric Roisin, Claus & TGT Catalysts Business Line Manager
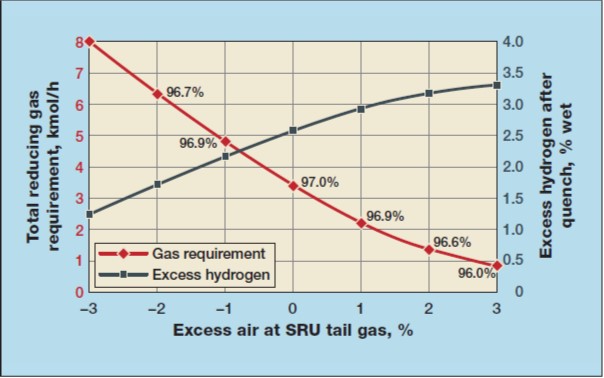
The presence of heat stable salts does affect the performance of the amine solvent,1 consequently H2S slip from the absorber may increase dramatically. To bring the H2S slip back to acceptable levels, the amine solvent needs to be restored back to pristine conditions, either by a reclaiming process or by partial or full replacement.
Reviewing the results of the amine analysis and focusing on the main identified heat stable salts should help in understanding the root cause of the problem. Let us assume that the involved amine is used exclusively to treat the outlet gas of the quench column downstream the Claus tail gas hydrogenation reactor, and that heat stable salts are mainly thiosulphates (but may be also sulphites or sulphates). Such species are likely formed because of the abnormal presence of SO2 in the feed gas to the absorber, assuming that there is no possibility for oxygen to contaminate the amine.
SO2 should have reacted with hydrogen on the CoMo catalyst. A breakthrough of SO2 from the reactor can only result from three potential causes:
- Hydrogen deficiency: each mole of SO2 feeding the reactor requires 3 moles of H2 to be transformed into H2S on the catalyst. Since the amount of SO2 in the Claus tail gas does vary over time, so does the hydrogen requirement. In case hydrogen is missing, SO2 breaks through. In case no SO2 analyser is installed to detect it, SO2does have consequences for the operation of the quench column: drop of pH, higher caustic consumption, corrosion of internals, filtration of solid deposits. As a safe operating guideline, Axens recommends maintaining the hydrogen concentration measured at the outlet of the quench column above 2.5 mol%. If the measured hydrogen partial pressure is too low, some designs include a trim line of hydrogen to adjust it. Another possibility to mitigate the risk of lacking hydrogen at the hydrogenation section is to operate the Claus furnace slightly deficient in air (meaning less SO2 feeding the TGTU) by targeting an H2 S/SO2 ratio out of the Claus section higher than 2 (typical target 4 to 6). Refer to the Figure on the left.
- Poorly performing catalyst: the first indicator would be the temperature profile across the bed since most of the temperature rise should occur on the top section of the fresh catalyst bed, moving down as the catalyst ages or gets contaminated (usually by soot or oxygen coming from the upstream reheater). There are two types of hydrogenation catalysts: older generation which need to be operated at an inlet temperature higher than 270°C (520°F), while some more recent products can be operated colder, down to 200-240°C (390-460°F) inlet. In case the performances of the catalyst are suspected to be insufficient, increasing the inlet temperature by 10-20°C (20-35°F) may solve the problem, if allowed by the installed reheating equipment.
- Catalyst bypass: a leaking feed effluent heat exchanger, or a channel across the catalyst bed (rupture of catalyst supporting grid, movement of catalyst in the reactor due to inhomogeneous gas distribution, equipment left inside the reactor during loading) would also result in a fraction of the Claus tail gas feeding the quench column.
References
- Sivasubramanian R H, Weiland M S, Effect of Heat-Stable Salts on Amine Absorber and Regenerator Performance, AIChE Meeting, Austin, TX, USA, 7 Nov 2004.
- Crevier P P, Roisin E, Klint B, Cundall M, An Assessment of Reducing Gas Production and Demand in the SRU/RTGU - How much is enough and what does the RGG contribute?, Laurance Reid Gas Conditioning Conference, Norman, OK, USA, 21-24 Feb 2010.
Get the latest news about Proven Solutions in Oil Refining
Subscribe to our business newsletter to keep up to date with Axens news.
This newsletter gives access to our experts' insights and the opportunity to stay up-to-date with our latest products, technologies and services.