First published in PTQ Q3 2020
Nicolas Lambert, Technology Team Manager – RDS, FCC & Sweetening Segment, Axens
Thibault Reffet, Technology Team Manager – Clean Fuels, Axens
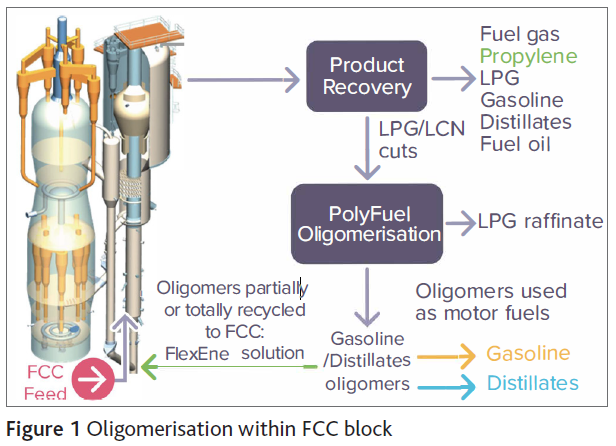
Beyond the obvious adjustments to the catalytic systems to include ZSM-5 and follow closely the latest catalytic developments, some upgrades on the technology side are possible. The principal hurdle will be the hydraulic limitations of the unit which could require reducing the unit throughput to achieve better performance.
Not so recent, but efficient in generating some margin in an existing unit, which can in turn be used to increase unit severity, is the FCC Alliance Stripper Packing. This largely proven equipment aims at thorough stripping of spent catalyst under all circumstances in the unit. Through an important reduction of hydrogen content in coke (versus disc and donuts, baffles, or other technologies), the air demand and regenerator(s) temperature are drastically reduced. Temperature drops of 10-15°C are routinely achieved, and possibly more depending on the starting point. The ‘room’ thus freed in the regenerator enables increasing the ROT in order to reach higher propylene yields.
Some other technical elements offered by the FCC Alliance and Axens have similar effects, albeit to a lesser extent:
- Feed injectors: FIT G-Series or FIT R-Series (depending on the unit feed diet) will reduce coke production through better, more intimate contacting of the feed. The liquid hydrocarbons are more efficiently and quickly vaporised to promote vapour phase cracking in order to limit coke formation by deposition on the catalyst. Following the same principle as above, reduced demand on the regenerator side allows increased severity
- The RS2 riser termination device will ensure minimum thermal degradation. The same load on the wet gas compressor can thus be achieved at the same unit throughput but operating at higher severity to promote propylene production
- MTC Technology: a riser quench that will force an increase in the catalyst circulation rate, bringing more energy to the riser and thus improving feed vaporisation and performances
In addition, if the LCN or external olefin-rich cuts can be disposed of, coupling the FCC unit with an external oligomerisation unit will prove a very efficient substitute to a secondary riser.
Indeed, the principal pathway for propylene from LCN cracking is through the intermediate oligomerisation of olefins subsequently followed by cracking. Cracking of paraffins requires much more energy for limited results. Externalising the oligomerisation step through Polynaphtha or PolyFuel processes will ensure a much higher extent of this reaction step, leaving only the cracking part to be performed by the cat cracker. In such a case, only oligomers are recycled to the FCC unit, requiring far less space than the full LCN cut, for instance, for much better results.
Moreover in addition to the LCN, the oligomerisation unit can convert the C4 olefins into oligomers that can be cracked to propylene. Hence, by using this type of technology, it is possible to tune the FCC product slate towards the desired products. This coupling of FCC with an oligomerisation process is called FlexEne (see Figure 1).
Get the latest news about Proven Solutions in Oil Refining
Subscribe to our business newsletter to keep up to date with Axens news.
This newsletter gives access to our experts' insights and the opportunity to stay up-to-date with our latest products, technologies and services.