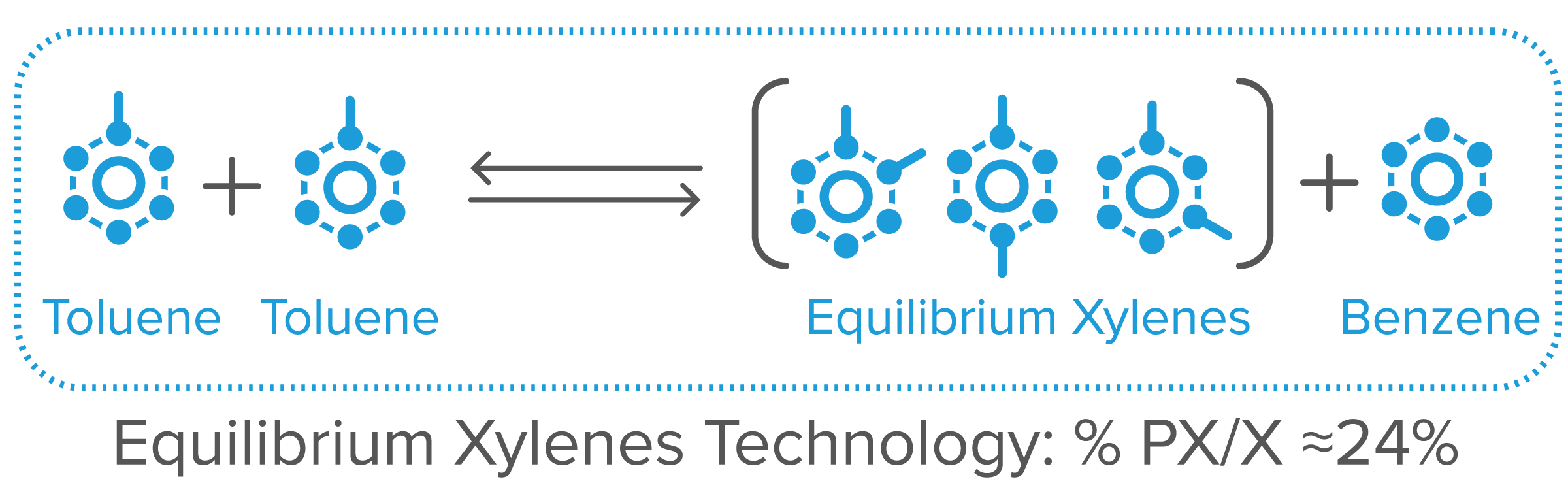
Search Axens.net
Process Technologies
process_technologies
Solutions - Advanced Process Licensing Solutions
Conference
Online - CDT
2 days
Speakers
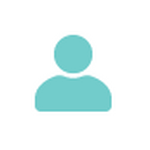
Matt Hutchinson
Senior Technology Manager, Gasoline and Petrochemicals
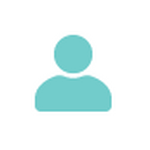
Mukund Yallambalse
Business Development Manager, Refining & Petrochemicals
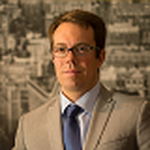
David Schwalje
Emerging Market Development Axens Americas
+1
IRPC Process
IRPC PROCESS TECHNOLOGY, an innovative virtual conference designed with current needs in mind. Held 2-3 June 2021, IRPC Process Technology will provide a platform for knowledge-sharing, networking and making business connections with downstream leaders—all from the safety and comfort of your home or office.

Renewable Fuels & Bio-Based Chemicals
Cellulosic Ethanol
Renewable Diesel and Jet
Lipid Feedstock
Lignocellulosic Biomass
Process Technologies
Americas
+6