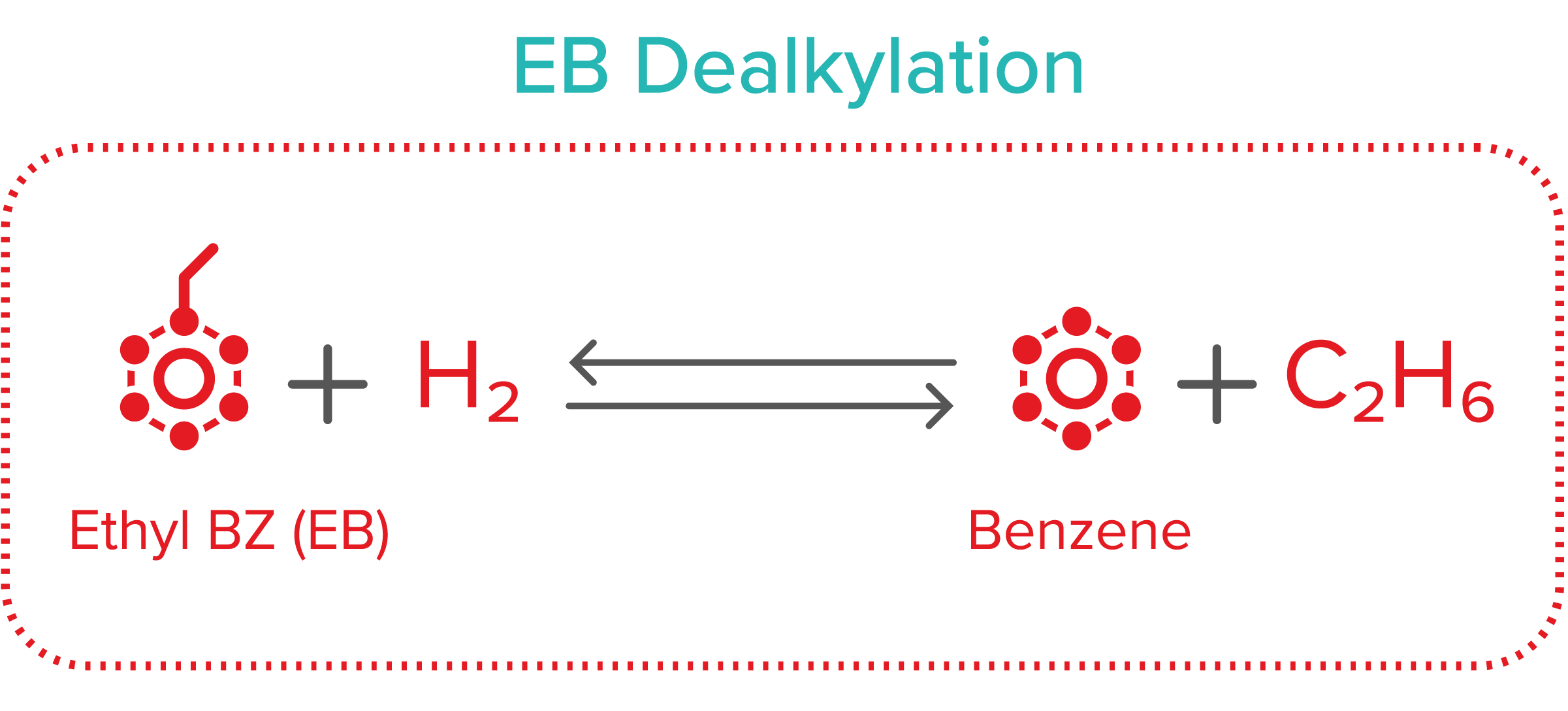
Search Axens.net
Process Technologies
process_technologies
Solutions - Advanced Process Licensing Solutions
Conference
Online - EDT
5 days
Speakers
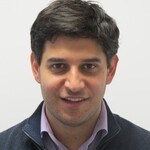
Alexandre Javidi
Business Developer leader for alcohol to Jet
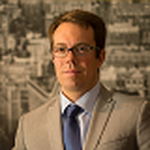
David Schwalje
Emerging Market Development Axens Americas
ABLC Digital 2021
At ABLC Digital, content is the catalyst that creates focused and meaningful opportunity through networking.