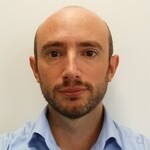
Search Axens.net
Process Technologies
process_technologies
Solutions - Advanced Process Licensing Solutions
Conference
Online - CEST
1 day
Speakers
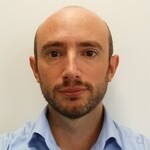
Clément Salais
Low Carbon Solutions Product Line Manager
GPA Europe Virtual Series 2021
GPA's virtual conference series promoting a new energy future and the transition of our industry towards that future.