Search Axens.net
Process Technologies
process_technologies
Solutions - Advanced Process Licensing Solutions
Conference
Online - EDT
5 days
Speakers
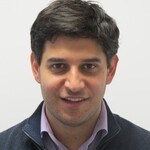
Alexandre Javidi
Business Developer leader for alcohol to Jet
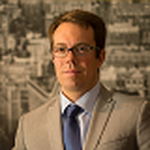
David Schwalje
Emerging Market Development Axens Americas
ABLC Digital 2021
At ABLC Digital, content is the catalyst that creates focused and meaningful opportunity through networking.
Conference
Online - CEST
4 days
Speakers
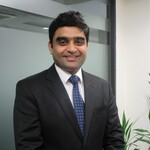
Varun Ginotra
Business Development Manager – Renewables Business Group
EUBCE 2021
EUBCE is the largest biomass conference and exhibition in the world. Each year, EUBCE brings together the greatest minds and latest advancements in biomass, with the aim of accelerating research and market uptake across the globe.

Renewable Fuels & Bio-Based Chemicals
Cellulosic Ethanol
Renewable Diesel and Jet
Lipid Feedstock
Lignocellulosic Biomass
Process Technologies
Europe
+6