Search Axens.net
Process Technologies
process_technologies
Solutions - Advanced Process Licensing Solutions
Conference
Online - CEST
2 days
Speakers
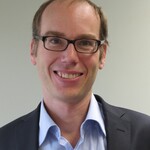
Nicolas Menet
Plastic Recycling Business Development Manager
Conference
Online - CEST
3 days
Speakers
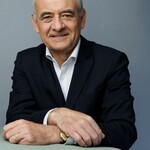
Jean Sentenac
Chairman of the Board
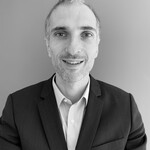
Vincent Duverne
Business Development Manager Gas Treatment / CCS
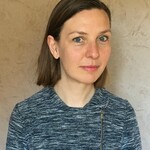
Madeleine Mitschler
Technologist, Renewables Group, Process Licensing Business Unit
+1
ESF 2021 - Energy & Sustainability Forum
2020 has accelerated the pivot to sustainability. At the core of conversion, refiners and petrochemical producers must responsibly and proactively transition from oil processors to energy providers, creating the products and services that today’s consumer still values.