First published in PTQ Catalysis 2022
Yoeugourthen Hamlaoui, Global Market Manager, Axens
Edouard Barange, Olefins Product Line Manager, Axens
Several cuts are valorised downstream of the steam cracker furnace. The heavier fraction corresponds to the pyrolysis gasoline, also known as pygas. Raw pygas contains highly valuable components such as BTX (benzene, toluene, xylenes), unsaturated compounds like diolefins, styrenics and olefins, and sulphur-containing compounds.
Depending on the feed quality, the catalyst used in the pygas first stage could either be palladium based or nickel based.
For a feed highly contaminated with metal such as arsine, mercury, silicon or lead, nickel based catalyst is recommended as the metal contaminant resistance is higher than the resistance allowed by palladium based catalyst.
However, in operation, some rapid catalyst deactivation episodes can be observed in pygas hydrogenation units.
Let us define first the different types of contaminant that could be present:
- Inhibitors or activity moderators that compete with reactants for catalyst active surface. As the adsorption is reversible, the catalyst activity is recovered once the contaminant is no more present in the feed without any specific treatment
- Temporary poisons with strong adsorption on the active surface of the catalyst. The catalyst activity is recovered with specific treatment (hot H2 stripping/regeneration), which requires a shutdown of the unit
- Permanent poisons with very strong adsorption on the active surface of the catalyst. The catalyst activity cannot be recovered.
Among these contaminants, arsine, silicon, sulphur species, oxygenates compounds, free water, gums may often be found in the pygas feed.
These contaminants may be carried out by the cracking furnace feed or/and the process itself. For example:
- Free water could come from an issue relative to the operation around the raw pygas storage tank or the operation of the caustic tower
- Silicon can be brought by injection of anti-fouling chemical agent upstream
- Metal contaminants come mainly with the steam crackers feed.
Contaminants that could have a drastic impact on catalyst activity, causing a rapid deactivation, are free water (free water combined with caustic soda is a temporary poison) and sulphur species. Indeed, pygas feed may contain up to several hundred parts per million of sulphur. Speciation of sulphur, including CS2, has highlighted the presence of thiophenes (80 wt% of the total sulphur species), mercaptans/sulphides/disulphides (15 wt%), CS2 (5 wt%), and H2S/COS (below 0.5 wt%).
These sulphur species have different poisoning effects on the catalyst. Among the sulphur species described here, thiophenes present the lowest poisoning effect, followed by mercaptans, sulphides, and disulphides in ascending order. H2S/COS has the strongest poisoning effect, and CS2 has the second strongest.
Another source of contamination is the H2 make-up used in the pygas first stage, where CO is the most common one acting as a strong inhibitor. High CO could occur with methanator upsets.
At a glance, rapid catalyst deactivation in pygas units is often explained by contamination issues that can be mitigated by a better understanding of the operational constraints and closed monitoring of the feed quality and upstream operation. These could be combined with a well-adapted loading diagram including adsorbent, grading, and catalyst to ensure the longest cycle length possible.
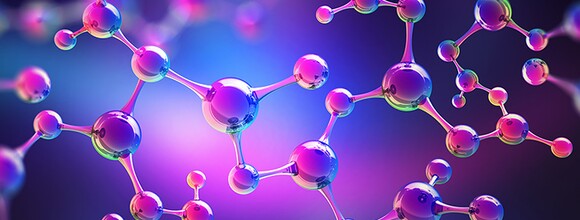