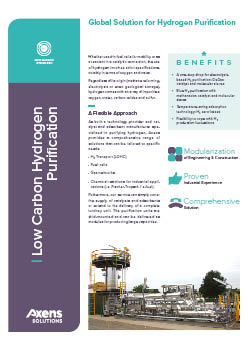
The decarbonization of industries that emit large amounts of CO₂, such as cement, steel, incinerators, pulp and paper, biomass boilers, refineries, and chemistry, can be addressed by capturing and converting the CO₂ into renewable or low-carbon fuels.
This process relies heavily on low-carbon electricity (used to produce hydrogen), which is then mixed with CO₂.
As a result, the final life cycle analysis of these fuels shows a lower carbon footprint. This approach offers a solution for decarbonizing the transportation sector, including maritime, aviation, and both light and heavy-duty vehicles.
Axens offers a comprehensive range of technologies, including Carbon Capture (DMX™, Advamine™), Reverse Water Gas Shift (Carboverseo™), CO₂ conditioning, H₂ purification, Fischer Tropsch, and Upgrading (Gasel®), to convert CO₂ into renewable/low-carbon fuels at low operating cost.
Furthermore, the more stringent specifications are met with a diverse range of products allowing the purification of CO₂, Syngas and H₂. The RWGS and Fischer Tropsch catalysts are protected against poisoning and deactivation.
The bankability of your project is guaranteed through a single point of contact, strong research and development support, and integrated guarantees.
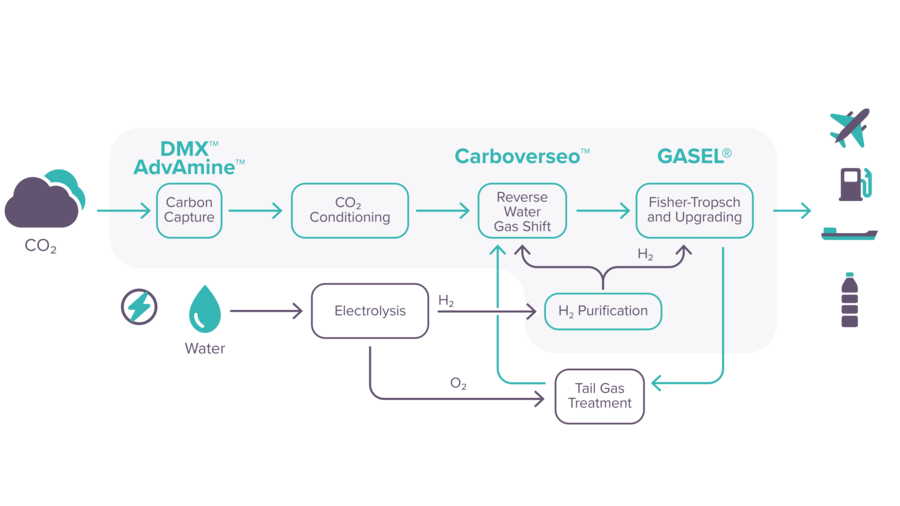
-
Integrated and innovative technologies and products (catalyst & adsorbents) to enhance the profitability of your low-carbon projects
-
With a single point of contact, Axens takes full responsibility for the project, improving its bankability.
-
From conceptualization and feasibility studies to basic engineering, start-up, and operation, Axens is the ideal partner to support your decarbonization projects.